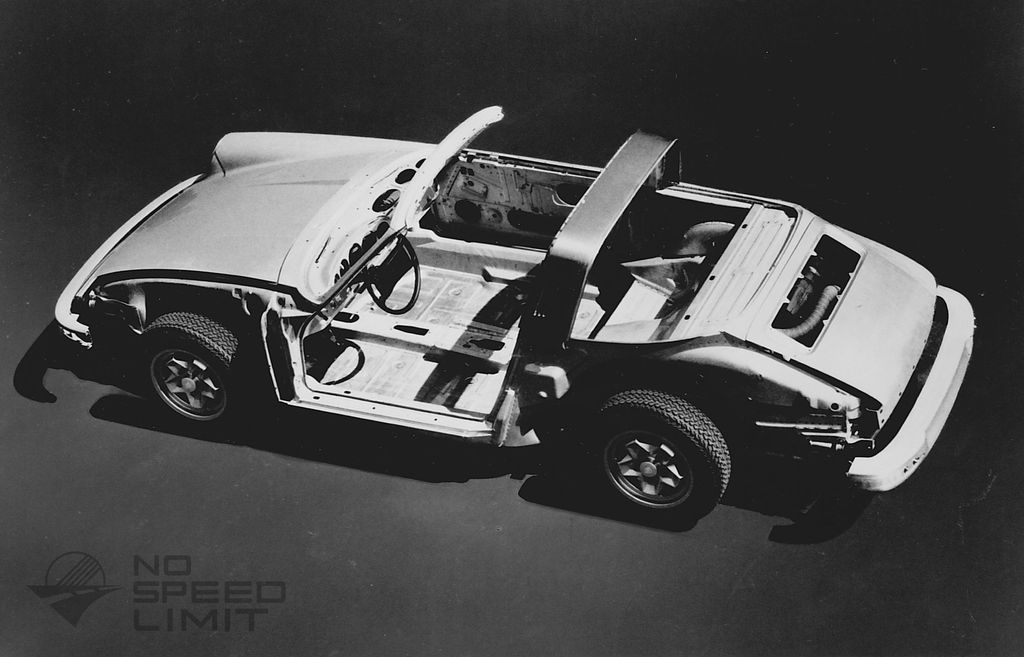
Thyssen and Porsche join forces
The lighter a car is, the less energy it uses to achieve a certain performance. And the longer a car lasts, the better the energy required for its production is used - from the raw material to the finished car.
That is why Porsche and Alusuisse/Alusingen are pursuing the Porsche aluminum body study project. At the 1981 International Motor Show in Frankfurt (September 17th to 27th), Alusuisse/Alusingen presented this project, developed jointly with Porsche: a 928 body made exclusively from the new "Anticorodal-120 R" alloy. This body shell, which weighs just 161 kg, offers a weight advantage of 106 kg compared to the partially aluminum body of the standard Porsche 928, and even 141 kg compared to a comparable all-steel version.
Porsche has calculated that a vehicle based on this body study, taking into account the manufacturing energy and with extensive recycling, would save the energy content of 1,500 to 2,000 liters of fuel over a driving distance of 300,000 kilometers compared to a conventional steel body. In practice, the use of all-aluminium bodies compared to conventional steel bodies could result in an annual mileage of 35,000 kilometres at today's petrol prices (August 1981 around 1.60 DM/litre of premium petrol ... note: around 1.90 Euro/l in 2024), depending on the vehicle size can save up to 400 DM per year (note: around 480 Euro in 2024).
The all-aluminum body represents a contribution to the discussion about future body concepts. Based on the findings available so far, aluminum as a body material is expected to have good future prospects in terms of possible weight savings, the overall energy balance, recycling and corrosion behavior.
The joint scope of work includes the following basic studies, the results of which are available in work packages:
"Porsche aluminum body"
Anticorodal 120R/AlMgO,4Si1,2
161 kg
Two-part longitudinal member as a repair-friendly solution in 1.75/2.00 mm.
Multi-part wheel arch for forming and strength reasons.
Use of an extruded aluminum profile to increase rigidity and operational strength as well as passive safety Cross sections remain unchanged for reasons of space.
Enlargement of the cross sections by raising and widening the supports (without changing the body cutouts).
Widened from 12 mm to 16 to 20 mm in order to be able to spot weld with the larger electrodes required.
Porsche Development Center Weissach (project management and prototype)
Alusuisse/Alusingen (Anticorodal 120R)
A. Läpple, Heilbronn (tools and forming technology tests)
Sciaky, Paris (welding technology)
Thyssen and Porsche join forces
Porsche 928 GTS
Porsche Press kit
Porsche Literature
Our Porsche Cars